Value Chain Mapping
GETTING STUCK WITH SIMILAR ASSIGNMENT? ENROL WITH EXPERTSMINDS’S VALUE CHAIN MAPPING ASSIGNMENT HELP SERVICES AND GET DISTRESSED WITH YOUR ASSIGNMENT WORRIES!
Question 1: Draw a Value Stream Map for table assembly process. Show all material flows, information flows and inventories. Draw a timeline showing processing times and waiting times.
Answer:
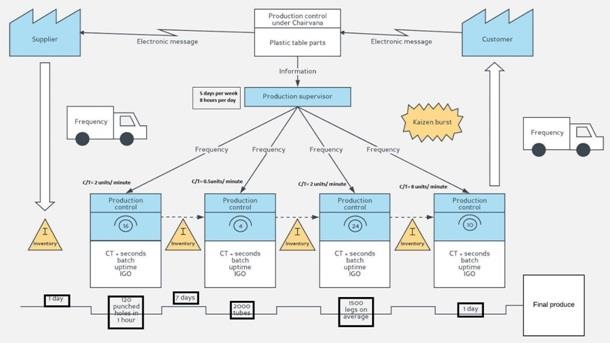
Diagram: Value Stream Map For Chair Assembly Process
Value stream mapping is mostly used to describe the method of lean management for analyzing the current state and designing a future state. This diagram shows the value stream of chairvana and it focuses on the area of the firm that add value of products or services.
Question 2: Calculate the Takt time in minutes for the table assembly process.
Answer: Takt time for table assembly operation
Takt time is often classified with the classic calculation
Available minute for production / required units of production = Takt Time
So according to the given data for construction the chair the time people works per day is 8hrs.
So: 8hours x 60 minutes = 480 total minutes.
However, there is a 10minute startup process and two breaks OF 10 minute each and at the end 15 minute of shutdown. That makes a total of 45 minutes. As this time is not in the production time, it is subtracted from "available time"
Therefore, 480 - 45 = 435
the leveled demand of the customer is 1000 per week. Therefore the demand for product each day would be:
1000 / 5 = 200 units of production.
DO WANT TO HIRE TUTOR FOR ORIGINAL VALUE CHAIN MAPPING ASSIGNMENT SOLUTION? AVAIL QUALITY VALUE CHAIN MAPPING ASSIGNMENT WRITING SERVICE AT BEST RATES!
Therefore, the demand for the chair is 200 units per day hence.
435 available minutes / 200 required units of production per day = 2.17 minutes (or we can even say 130.20 seconds)
Now the calculation for the week, rather than day is:
435 minutes (in One day) x 5 days(in One week) = 2175 total available minutes
2175 available minutes / 710 required units of production which equals 8.7 minutes (or 522 seconds).
Question 3: For each step of the process, calculate the cycle time in minutes and the capacity utilization.
Answer: • Cycle time for table hole punching:
• Minutes per part
Parts per minute = 1 / minutes per part
• Seconds per part
Parts per minute = (1 / seconds per part) x 60
• Hours per part
Parts per minute = (1 / hours per part)/ 60
• Parts per hour
Parts per minute = 120 / 60
Therefore,The cycle time for table hole punching is 2 units per minute.
For Leg bending
• Cycle time for leg bending:
• Minutes per part
Parts per minute = 1 / minutes per part
• Seconds per part
Parts per minute = (1 / seconds per part) x 60
• Hours per part
Parts per minute = (1 / hours per part)/ 60
• Parts per hour
Parts per minute =1 / 120
Therefore, the cycle time for table leg bending is 1 unitsin 120 seconds.
• Cycle time for Hinge assembly:
• Minutes per part
Parts per minute = 1 / minutes per part
• Seconds per part
Parts per minute = (1 / seconds per part) x 60
MOST RELIABLE AND TRUSTWORTHY VALUE CHAIN MAPPING ASSIGNMENT HELP & HOMEWORK WRITING SERVICES AT YOUR DOORSTEPS!
• Hours per part
Parts per minute = (1 / hours per part)/ 60
• Parts per hour
Parts per minute =1 / 120
The cycle time for hinge assembly station is 1 table in 2 minute.
• Cycle time for Footer assembly:
• Minutes per part
Parts per minute = 1 / minutes per part
• Seconds per part
Parts per minute = (4 / 30) x 60 = 8
• Hours per part
Parts per minute = (1 / hours per part)/ 60
• Parts per hour
Parts per minute =1 / 120
Therefore, the cycle time for footer assembly is 8 parts per minute.
8 x 60 = 480 parts per hour.
480 x 8 x 5 = 19200 per week.
Let us assume the maximum capacity is 20000 per week
Capacity Utilization= (19200/20000) x100= 96
• Cycle time for table assembly:
• Minutes per part
Parts per minute = 1 / 6 minutes
• Seconds per part
Parts per minute = (1 / 360) x 60 = 8
• Hours per part
Parts per minute = (1 / 360)/ 60
• Parts per hour
Parts per minute =1 / 120
Therefore, the cycle time for the table assembly is 20 / per hour.
20x5= 100 cycles per week.
Let us assume that the maximum capacity is 120/ week.
Capacity utilization (Weekly)= (100/120)x100= 83.33
Question 4: Calculate the total lead time and total processing time in days, hours and minutes.
Answer: The lead time is calculated by calcuting the elapsed time, wheresin cycle time the minutes, parts etc. is taken into consideration. The lead time a time duration that is calculated in terms of lead demand, and the safety stock or according to reorder point through the direct forecast.
The lead time and total time in days, hours and minutes is about 20 days. Of delivery from the inventory.
NEVER MISS YOUR CHANCE TO EXCEL IN ASSIGNMENT! AVAIL AFFORDABLE AND RELIABLE VALUE CHAIN MAPPING ASSIGNMENTS HELP SERVICES OF EXPERTSMINDS.COM!