Operations Management Case Study Assignment Help
You have been employed as a member of a production improvement task force for a Drive Shaft Manufacturing Company (DSMC). DSMC has been experiencing a severe backlog in sales orders due to antiquated machinery and poor production planning. The Company has just received an unprecedented contract to supply 450 drive shafts by the process given below. However, finances at present are tight and only £250,000 can be invested. Some of the order can be sub-contracted. Your task is to determine the maximum capacity of the current production line after the investment of the £250,000 hence how many parts must be made by the sub-contractor. The cost list of potential capital improvements is given on next page. The current output of the line averages 180 shafts on the two 38-hour shift system.
Save distinction marks in each Operations Management Case Study Assignment Help solution which is written by our professional writer!
Operations Management
Introduction
Production management is the process of combination of resources for manufacturing into organizing all value-added subsystems in a controlled manner. The transformation of resources into value added services and products (Jaramilloet al 2008). This case refers to the Drive Shaft Manufacturing Company that produces the driving shafts regularly to its clients. The current production capacity of the production line is 180 shafts on two 38 hour shift system per week. The machine hour capacity of a manufacturing plant is the well-established method to understand the production capacity.
Application of Lean management Theory
This case study applied lean manufacturing theories for the development of the process improvement plan optimal for the investment choice of 120000 GBP. Lean theory aims at the increase of the velocity of the operational process. Lean strategies offer tools to identify the process delays by thoroughly analyzing the process flow. The main objective of this theory is to demarcate value-added and non-value added elements within the process flow. Profitability and productivity are the two important variables for manufacturing industries. Innovations are an essential part of the production of any organization. In this case, components are manufactured as bulk at a time in a few dedicated areas of cells. Based on the lean theory, careful monitoring is done to every single unit in the process. Lean implementations in this field are primarily focused on the elimination of waste in staffing and staff processes. Services industries typically spend a larger percentage of operating expenses on overhead and labor costs. (Desai t al 2010)
Description
The current plant capacity is calculated by the total number of hours multiplied by the total number of machinery employed in the production. The case reveals that two 38 hour shift is required to generate 180 products.
No of driving shafts = 180
No of work hours = 38 x 2 = 76 hours
For the production of 450 shafts, 76/180 * 450
No of work hours required = 190 hours
No of machinery = 12
The total factory capacity is 12 x 76 = 912 hours
The current factory capacity rate is very low to produce the 450 driving shafts
Capacity utilization rate is the measure used to calculate the rate of at which probable output levels would be achieved. It is also called as an operating rate.
Capacity utilization rate = Actual output/potential output x 100
In this case, the actual output is 180 and the potential output expected is 450. Hence, Capacity utilization rate = 180/450 x 100 = 40%. The lower capacity utilization rate indicates that this business is currently performing very low.
The company is currently interested in investing 120000 GBP for improvement of the process. The low capacity utilization rate indicates the demand for the process improvement by investing in new machinery and labor to reduce the time taken for operation and increase the efficiency of the operation. Lean implementations in this field are primarily focused on the elimination of waste in staffing and staff processes. Services industries typically spend a larger percentage of operating expenses on overhead and labor costs. This can account for 50 percent of the operating costs while inventory is in the range of 2 percent as compared to manufacturing.
The key weaknesses observed in the current production line are
1. The saw machine requires two blades, blade A and blade B, with frequent blade replacement for 40 and 30 respectively. The maximum repair time of this machine is 30 minutes.
2. The labor for product inspection is insufficient since only one inspector checks only one block to assess the quality of block coating with the rejection rate of 20%.
3. The current hardener used in the process is consuming time with less capacity.
4. The gear cutting machine has mean breakdown time 5000 requiring tool change for every 100 parts. This machine adds the cost of material for tool change and repair.
5. The plating process consumes 36 minutes to plate 36 product parts. The operation totally consumes 72 hours before and after placing it in the buffer and 4 hours are lost every week for changing buffers. Hence, this process decreases the efficiency of the production
The production line is described using the Kanban method where three employees are recruited for the total production of the drive shaft.
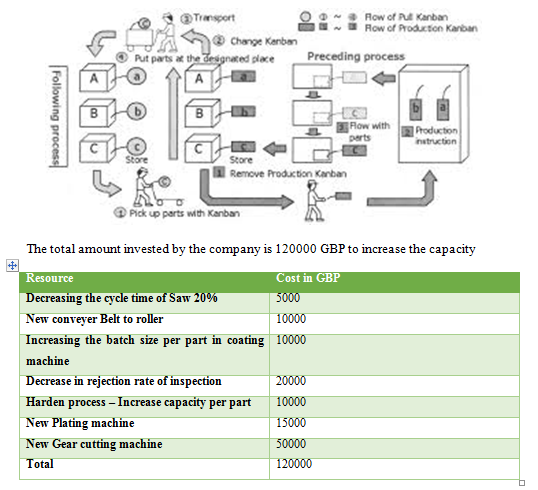
According to (Radnor 2010), there are five key principles in the lean production theory namely
1. Definition of value for each product
2. Elimination of non-value added steps in the production process
3. Establishment of productive work valuable flow
4. Customer demand based pull production activity
5. Pursuing perfect production continuously
Discussion
The purchase of the above resources from the new budget would increase the capacity of the production line and decrease the warm-up time. The number of operators working per line is not increased in this case whereas machinery and tools which decreases the time and increases the cost are replaced with the efficient ones. From the lean theory, this process plan was developed aiming at decreasing the setup cycle time and new machinery was planned for procurement aiming at the increasing the productive efficiency of the process. The Lean theory suggests a close partnership with the suppliers will still more render the operations productive without delay in this shift system. The Lean theory also suggests that a skilled and trained workforce plays an immense role in the continuous development of organizational productivity and turnover (Hsuet al 2007). Hence, skilled labor is also hired reducing the rate of rejection during the inspection of the drive shaft quality.
The main focus of this plan involves decreasing the rejection rate of products, increasing the batch size promoting the mass production for machines and finally resources required to decrease the cycle time. In this plan, the total time taken for production of unit is reduced to 30 hours. The cycle time of saw is reduced to 20% which reflects the increase of capacity to 20 parts per cycle. The new conveyer belt carries 200 parts to the coating and cycle time is reduced from 60 minutes to 20 min. The increasing in batch size for coating directly accommodates 200 parts from the conveyer to coating machine to complete the coating process. The reduction of the rejection rate in the inspection is 50% that increases the capacity of the production line. Lean strategies offer tools to identify the process delays by thoroughly analyzing the process flow. The main objective of this theory is to demarcate value added and non-value added elements within the process flow. Profitability and productivity are the two important variables for manufacturing industries (Desai et al 2010)Innovations are an essential part of the production for any organization. The hardening process is subjected to capacity increase decreasing the cycle time as well as cut the process time to 10 minutes. The new gear cutting machine reduces the cycle time to 2 minutes. The new plating machine reduces the cycle to 15 minutes. The new packaging line reduced the overall packaging time to 0.5 minutes for 200 driving shafts. Hence for a total 450 shafts requires 1.25 minutes. The line efficiency of the total product line is estimated as total minutes taken in production line x 100/ Total time attended by operators
Line efficiency = 5700 minutes/ 80 minutes x 100
Line efficiency = 71%
Line Efficiency is one the chief marker of the maximum output capacity of the production line. The new process improvement plan has 71% line efficiency. The capacity utilization rate is estimated as the actual output/potential output x 100. The potential output of the newly proposed production line is 600.
Capacity utilization = 450/600 x 100 = 75%. Hence the newly proposed process improvement plan has 75% capacity utilization rather than the old one that has 40%.
The measure of productivity is described as total process output per single unit for total input. Development of the production model is a numerical expression of the manufacturing process using price data. This plan was developed using the price data given in the case study. Only machinery and skilled labor essential for the process were planned for the procurement. For example: Inspection process was delayed too much due to lack of proper machinery, skilled workforce. It is always advisable to examine the entire phenomena before the development of process improvement. After calculating the capacity utilization, line efficiency and other capacity factors, it was observed gear cutting, packaging, sawing and inspection process has delayed setup time and high error rates due to outdated machinery and lack of skilled workforce. Hence, the process improvement plan was developed focusing on the procurement of machinery that reduces the error, increase the production efficiency at less cycle time. (Desai et al 2010)
Another chief factor that plays an immense role in the upregulation of production efficiency is the better or proper use of available resources. For example, the grinding machine buffers are too expensive and shall not be wasted for error bars and hence reducing the error rate during inspection is essential for reducing the cycle time and non-wastage of machinery as well as material resources. Smart use of resources usually reduces the cost of operation for the manufacturing organization. (Gant, 2007) The chief applications of the lean production method in this manufacturing industrial market include
1. To ensure that products are developed to cater to the needs of the customer
2. Removal of non-value added products within the production process
3. Reduction of error rate during the product development at every single unit of process flow
4. Reducing the cycle time at every single unit of the production
5. Delivering an accurate product
A relative intricacy arises when the whole process is applied with lean principles which require disaggregation of the whole process and flowed at different functional regions of production. In this case, no disaggregation of the process flow is permitted since the replacement of outdated machinery and hiring one additional skilled labor definitely do not disturb or change the process flow. Truly speaking, the interrelationship between processes adds cost developments dedicated to the overall operation. This method is especially effective for an implementation team in the initial stages of problem exploration. The application of this strategy involves asking a series of "why-related" questions to drill down into a problem area. Asking progressive questions about a perceived difficulty forces team members to think critically about the actual sources of waste and inefficiency. It is suggested that at least five questions (5-Whys) are posted in order to arrive at the root cause of the problem. (Desaiet al 2010)
Conclusion
The transformation of resources into value-added services and products. This case refers to the Drive Shaft Manufacturing Company that produces the driving shafts regularly to its clients. The current production capacity of the production line is 180 shafts on two 38 hour shift system per week. The current process improvement plan is aimed at increasing the maximum output by reducing the total cycle time, purchasing new resources to increase the efficiency and finally to increase the capacity of the production. The overall time taken for production of 450 shafts is reduced from 190 hrs to 95 hours by investing 120000 GBP. Lean strategies offer tools to identify the process delays by thoroughly analyzing the process flow. The main objective of this theory is to demarcate value added and non-value added elements within the process flow. Profitability and productivity are the two important variables for manufacturing industries. Innovations are essential part of the production of any organization. The conveyor machine, coating machine, hardening process capacity was increased by reducing the error and cycle time taken. Moreover, the batch size for the production is increased.
Most reliable and trustworthy Operations Management Case Study Assignment Help & Homework Writing Services at your doorsteps!