MECH 0011 Manufacturing Technology and Materials Assignment Help
The students produce a feasibility study for a new product. This feasibility study should comprise a specification for the product and a commercial justification for its further development. The study should introduce the product along with its main function, then, it should explain the material history for the product and the reasons behind this development at each stage. The student may select any product, however, the complexity of the study will have an immense effect on the assessment process. The students must demonstrate their claim that the product has value and marketability.
Get ready to submit MECH 0011 Manufacturing Technology and Materials Assignment Help solutions – 100% plagiarism free work document at nominal charges!
Topic : MULTI PURPOSE ABRASIVE BELT GRINDER
Multi purpose abrasive belt grinder
The machine we tend to designed and fictional will be applied for grinding any form of object like circular, square,prismitical, two-dimensional figureof any range of facet.. It will simply grind any variety of form simply. It's a helpful product for grinding purpose. In our project the work abrasive belt is employed to grinding the fabric. The abrasives belts are started amnd revolved by the one section induction motor.
Then our assignment particularly abrasive belt grinder may be a special variety of machine. Consistent with the sort of fabric to be grind.it is straightforward to alter of any a part of it.
This assignments gives details of grinding numerous shapes and sizes of element. This machine will be widely applied in most variety of industries. By dynamic's the block sizes we will get a better finishing speed of over 11000 rate if it is required.
Introduction
:
it is applied to grind the machining surfaces to super finishing with accuracy.it will be applied for outwardly grinding by fixing the belt grinder attachment on the conveyor roller. The principle componentsof this machine square measure listed in discription and fabrication half.
Concept:
the belt of abrasive is employed for grinding the fabric. This abrasive's belt is operated by the one section induction motor. This whole assembly is assembled on the frame structure wherever the part assembled.
The roller wheel is assembled on the 2 finish bearings with bearing cap by appropriate assembly. There square measure 2 roller wheel is employed in our assignment to operatethe belt of abrasive. One facet of the roller wheel shaft, one v-pulley is joined by the acceptable means that. Thatonesection induction motor with v-pulley assembly is employed to operate the abrasive's sheet or belt through the some specific bet driving mechanisms.
Description and fabrication of elements
1. Main frame structure
2. Roller shaft.
3. ‘v' pulley
4. Bearing cap with bearing
5.Abrasive belt
6. Roller wheel
7. Single section induction motor
1. Main frame structure:
this is fabricated from soft-cast steel material.
tha entire component square measure assembled on this structure with the acceptable assembly.. Making of bearing diameter and open bores drained one setting therefore one aligns the bearings properly .
2. Roller shaft:
this can be machined as per the drawing. One finish is machined to carry the ‘v' belt block and therefore the alternative finish is fastened to the frame structure. Middle portion is machined to suit the bearing as a roller wheel. This roller with bearings is assembled in main body. This roller are revolved through the ‘v' belt block throughout the operation.
3. ‘v' pulley:
this can be fabricated from c.i material and machined to straightforward kind if single ‘a groove. Roller is revolved by the motor through this block and ‘v' rope. Diameter of this block is style to run the spindle regarding 2000 rate.
4. Bearing cap:
this can be fabricated from soft-cast steel material. This can be machined as per the drawing. This covers the bearings and conjointly tights the bearings with the most body by fastening
Bearings:
this can be a regular size hall bearing no.6202 nbi. This can be alter the roller to rotate and wear the load sleek and stiffly.
5. Abrasive belt:
this abrasive belt is factory-made in numerous grades. We've got to pick the grades consistent with the fabric that we've got to grind.
6. Roller wheel:
this can be fabricated from soft-cast steel material. There square measure 2roller is employed to drive the abrasive belt.
7. Single section induction motor:
it's found to drive the roller shaft that fastened on the tip of the frame structure. The free finish of the shaft within the motor an outsized block is found around that the belt runs. The opposite specification concerning the motor is mentioned in style a part of the machine.
The main difference is the various sorts of one-phase Alternative current motors is however they're going concerning beginning the rotor in a very specificdirection
1. Split-phase motors:
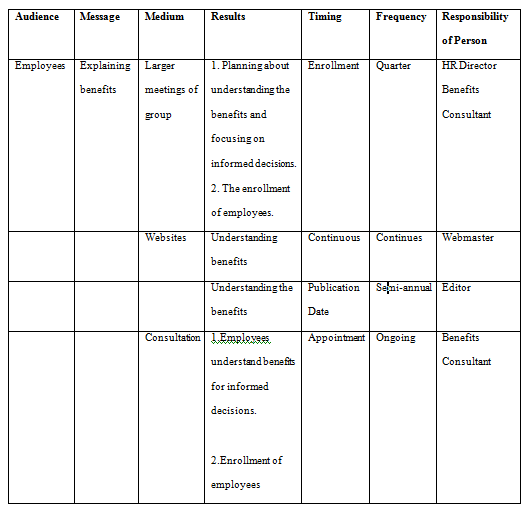
Material for abrasive belt:
Abrasive
The abrasive unit contains 2importanntsorts of abrasives.
SiC: it can be terribly not smooth and intensely arduous, however this is used as associate abrasives is restricted to many places by its crispness. Carbides ought to be employed of chipping of lower durable materials like gray robust, chilled iron, bronze, aluminium, copper, brass and non-metallic materials. A special kind of carbide, inexperienced in color, is employed to grind carbide-pointed tools.
AlO3: this can be comparatively not sharper than carbides however are way harder. It ought to be employed in the chipping of material having higher tensile strength like Steels, toughenedmalleable iron and robust alloys. There is conjointly another kind of corundum that is white in color as against the traditional brown selection. This white aluminiumoxidetends to fracture a lot of without delay than the regular (brown) corundum, and a lot ofand slicker cutting edges area unit thus conferred to the work. Grinding wheels of white aluminium oxide ought to be designated once grinding hardened tool steels or to be used normally tooling area
Grit size.
Construction
The stand (or) base is to hold the entire machine. The 2 conveyor roller is fastened to the 2 finishs of the frame stand with the assistance of end bearing (6202) with bearing cap. The conveyor roller shaft is coupled to the one section induction motor with the assistance of v-pulley and belt drive mechanism. This total arrangement is employed to rotate the abrasive belt from one place to a different place with the assistance of conveyor mechanism.
Bearings square measure coated by bearing cap that is welded to the frame stand. The motor block and roller block is connected by the v-belt drive mechanism. The abrasive belt is mounted on these 2 roller wheel so it'llrunning endlessly.
Working of unit
This machine is fastened on the work table, wherever the compound rest. Wherever the motor is on, the abrasive belt and therefore the roller wheel are revolved, on the rate of concerning. Job is persisted the hand, for instance, if we tend to grind a surface of a body, the abrasive belt are rotating on higher rate.
Depth of grinding is also given by cross slide, and therefore thelongitudinalmovement are given by manual feed. Usually depth per cut are zero.02 to 0.05 mm. The grinding stone is connected to the roller shaft so the emery wheel is revolved. The delicate grinding operation is completed with the assistance of emery wheel.
Design
design and drawings
design calculation: rate of the abrasive belt ought to be high.for this victimisation commonplacemotor having 1440 rate, the abrasive belt speed is reborn to higher rate.
Formula:d x rpm = d1 x rpm1
where,
d - the motor block diameter
d1 - main shaft block diameter
as per our style
d - 76 millimetre
d1 - 47 millimetre
motor rpm - 1440
therefore,
main shaft rate = (d x motor rpm )/d1
= (76 x 1440)/47= 2300 rpm
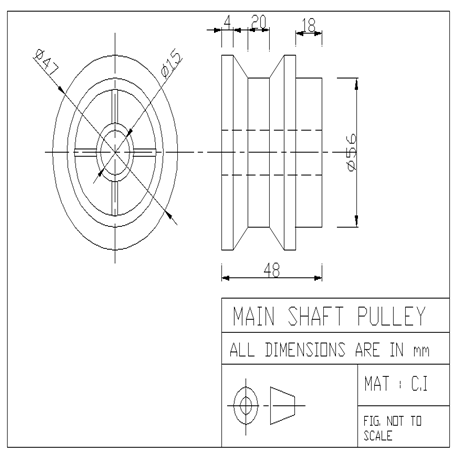
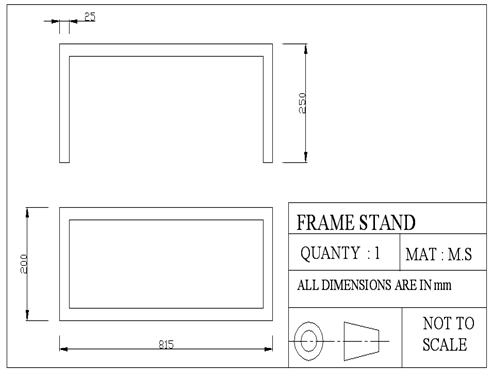
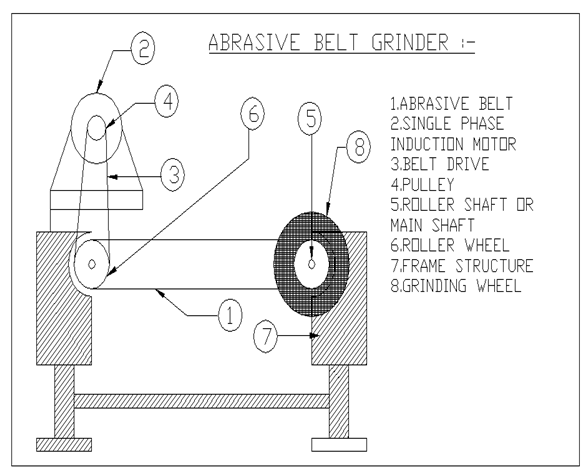
Advantages and drawbacks
Advantages:
1. The machine is compact and rigid in size.
2. Maintenance is a smaller amount.
3. It will be used on anyplace of little grinding application
4. By varied the block diameter the speed of the abrasive belt to be modified.
Disadvantages:
1.the abrasive belt ought to be changeable one for
completely different material. This method takes longer.
Applications
1. Grinding outside the work in any size of body will be done.
2. Because the feed is given automatic, 0.8 micrometer end is also achieved.
3. By dynamic the grades of abrasive belt grinding it will be accustomedgrind the steel, steel and chrome steel etc.
Field of application
where grinding end is needed it will be used. For instance, outer military intelligence of spindle of varies machines.
Cost estimation
sl. No. Partname material qtyamount(rs)
the part name and cost are given below:
1 roller wheel m.s 2 400
2 shaft m.s 2 200
3 abrasive belt abrasive 1 500
4 motor aluminium 1 2700
5 bearing steel 4 300
6 pulley m.s 2 150
7 v-belt rubber 1 300
8 bearing cap m.s 4 200
9 framestructurem.s 1 500
10 bolt and nut ---- ----- 100
11 fabricationcost ------ ----- 1000
total =6350
The total cost of this product is 6350.the fabrication cist is higher in comparision to other processes.
Conclusion
The assignment "design and fabrication of multi purpose abrasive belt grinder" is that designed and erected. The look and erection of this machine concerned a good deal of effort to create the assignment in and helpful. We tend to conclude the project report on "design and fabrication of multi purpose abrasive belt grinder"
Save distinction marks in each MECH 0011 Manufacturing Technology and Materials Assignment Help which is written by our professional writer!