Analysis of Cost and Feasibility Evaluation Assignment Help
ABC Inc is investigating the use of an automated machine to inspect the final product quality of their manufactured devices. The automated machine costs $17 million. It is available from the vendor in Florida in about two months. Costs of shipping from Florida is $50,000. Building modifications and installation costs are estimated at $130,000. Assume operating costs of the equipment is negligible. A trip to Florida for ABC Inc. folks to pre-inspect the automated machine costs $5,000.
Currently, ABC Inc. uses manual labor inspection. These workers cost an hourly wage of $35/hour. An inspector can inspect 7 devices per hour, and the product manager estimates that he needs 16 inspectors to inspect the items and complete production on time. They work 8 hours per shift, and 200 shifts per year are required. ABC Inc sells about 170,000 devices per year at a sales price of $75 each to the wholesaler.
There is also a risk of false negatives (15%) from the manual inspection, so the company actually pays the workers $25/ hour and sets the other $10/hour to cover cost of poor quality. This contingency is considered a regular business expense. The automated machine has an extremely low false negative rate of 2%, so no cash reserve is anticipated to be needed
ABC uses a planning horizon of four years and has a corporate MARR of 12%.
Need a pre-tax analysis of this situation
Need a recommendation whether the company should buy the automated machines based on the calculations.
Save your higher grade with acquiring Analysis of Cost and Feasibility Evaluation Assignment Help & quality homework writing services of Expertsminds.com
Step - 1
Calculation
Cost so involved is as under:
1. Cost of automated machine : $ 17 million
2. Shipping Cost : $ 50,000
3. Installation Cost : $ 130,000
4. Travelling cost for pre- inspection : $ 5,000
Considering the above cost elements, the total cost of automated machine, inclusive of travelling cost , freight or shipping and installation expenses, is $ 17,185,000.
Thus the total cost to procure the automated machine is $ 17,185,000.
The time horizon or planning horizon are 4 years, which is medium term horizon and is considered to be requiring to realize or and to recover or liquidate the cost so incurred in the acquisition of automated machine
Campbell R.Harvey, defines Planning horizon as a duration of time that leads a project into the future. However, according to Farlex Financial Dictionary, a plan that emerges into a future time. Likewise the time horizon or planning horizon for 4 years is adopted by ABC Inc.,
Considering the ABC Inc's time horizon plan, it appears to be less risky.However, the cost of automated machine is considered to be recovered/ liquidated at $ 4,296,250 per year for a period of 4 years.
Step - 2
Calculation of labor cost
Let us write down the required data to calculate labor cost as under:
ABC Inc needs to hire 16 inspectors
Hourly wages per inspector is $ 35 per hour which includes $10 towards risk of 15% false negative due to manual inspection and to cover cost arising out of poor quality.
Device or product that each inspector an inspect is 7 per hour
Number of hours of work per shift is 8 hours and 200 shifts are required for completion of production on time.
Hence,
Wages per inspector is $ 35 per hour
8 hours make 1 shift
Number of inspectors are 16
Thus, labor cost per shift is equal to 16 inspector multiplied by 8 again multiplied $ 35, wages per hour per inspector.
Consequently, it is 16 x 8 x $35 = $ 4,480 per shift
Total shifts added up to be required to complete the production on time is 200 Shifts per year. Accordingly, 200 shift x $ 4,480 = $ 896,000
Thus, labor cost per year to produce 170,000 devices is $ 896,000
ABC uses a planning horizon of four years and has a corporate MARR of 12%
Planning horizon is discussed above under Step No.1.
ABC Inc, has adopted MARR of 12%.
In simple words MARR is Minimum Acceptable Rate of Return and also called as Hurdle Rate
However, more often than not, few projects, capital investment in nature, adopt comparing IRR to MARR.
Under this circumstance, MARR should be more than or equal to IRR to proceed with project.
The hurdle rate , in short, is arrived at taking into account the significance of various aspects that pre exist and the risk factor attached with it. However facts that are relevant are being considered.
The hurdle rate is a cutoff rate, and identified with cost of capital
WACC is regarded as MARR in most of the company where, MARR is higher than or equal to IRR.
The generally accepted rate of MARR is 12%, and ABC Inc., has also considered 12% MARR.
And hence the MARR at 12% on $ 17,185,000.= $2,062,200.
ABC Inc sells 170,000 devices per annum at $75 each.
Thus the sale value will sum up to = 170,000 x $ 75 = $ 12,750,000
Step - 3
Analysis of profit
Following are the results arrived as per calculation under Step -1 and Step - 2.
They are as under:
1. The cost of automated machine is considered to be recovered/ liquidated at $ 4,296,250 per year for a period of 4 years as arrived at under Step-1
2. And labor cost per year to produce 170,000 devices is $ 896,000 as arrived at under Step-2
Before proceeding to pre-tax analysis, pre-tax income needs to be arrived at as given under:
Pretax Income formula is as under.
Pretax Income formula = Revenues- Expenses (Income Tax expenses excluded)
Therefore, if the above formula is applied, considering the expenses arrived at, based on available data as per ABC Inc.,
Profit under
Step- 1 is as under.
Let us find and analyze profit under step -1 using NPV and IRR as shown in the chart below:
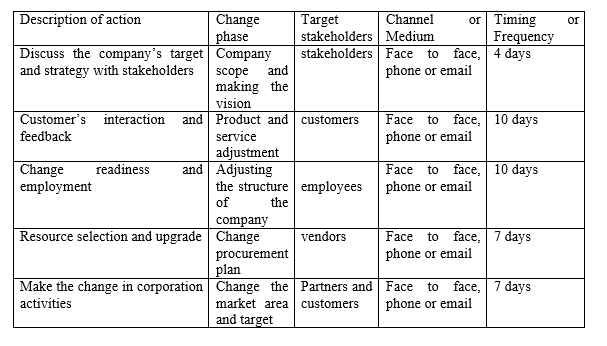
The finding recommends to pursue the project.
Profit under Step- 2 is as under.
Revenue = $ 12,750.000
Expenses = $ 896,000
Profit = $ 11,854,000
False negative = (15%) or $ 10 per hour as provided in the ABC Inc's data Let us consider, False negative at $ 10 per hour for 25,600 hour = 256,000
- [ 16 Inspectors * 8 hours per shift = 128 hours
- Cost of 200 shift = 200*128 hrs = 25,600 hrs
- 25,600 hrs x $ 10 = $256,000 ]
Pre-tax analysis:
If we make pre-tax analysis, profit under 2 , appears to be in a better situation than that of profit under - 1.
The reason being, in spite of having false negative under manual inspection, the value of such negatives is more or less equal in both case of engaging labor or automated machine unless we consider 15% as false negative under labor inspection which gives an alarming picture.
Recommendation
Based on the detailed analysis prepared above, it is recommended to continue with the manual labor to inspect the device rather than acquiring automated machine.
This will avoid any unpredictable or unforeseen risk resulting in adverse effect on the performance of the company.
However, it may please be noted , if false negative, which is 15% under labor inspection is considered, it is recommended to acquire automated machine as it saves a large amount of money from being lost .
Expertsminds.com accepts instant and short deadlines order for Analysis of Cost and Feasibility Evaluation Assignment Help service - order today for excellence!