GET ASSURED A++ GRADE IN EACH 7108IBA SUPPLY CHAIN MANAGEMENT ASSIGNMENT ORDER - ORDER FOR ORIGINALLY WRITTEN SOLUTIONS!
7108IBA Supply Chain Modeling Assignment - Griffith University, Australia
Learning Outcomes -
1. Understand the conditions and applicability of different supply chain models.
2. Apply common modeling techniques and optimization approaches for supply chain management.
3. Assess the trade-offs among different aspects of supply chain management, such as cost, time, and service level, and interpret the outputs from supply chain models.
Supply Chain Management Assignment: Dronautics Ltd., Australia
Case Study: This assignment requires analysis of supply chain logistics of the Su a drone manufacturing company operating with 3 manufacturing sites in Australia - Cairns, Darwin and Mandurah with per unit drone production costs being $43, $40 and $42 respectively. Drones are shipped in pellets or units to the distribution centers located in Adelaide or New Castle and in turn to 12 identified markets across the nation where there is high demand for the product. The study analyses and optimizes production and supply cost of the products and considers efficient allocation of resources to conclude on suggested networking channels in supply chain management.
Definition of Supply Chain: "SCM is the active management of supply chain activities to maximize customer value and achieve sustainable competitive advantage," (SME, 2017). The process includes all activities from product development to sourcing, logistics and coordination of information flow to achieve on time delivery results.
- It is a coordinated effort of multiple organizations representing each phase in a supply chain in delivering the product to an end user linked through physical and information flows
- The entire chain of activities is not limited to the warehouse or those within distribution centers or "the four walls" (Minhong Wang, 2009) . It is consideration of all factors such as allocation of time and resources to achieve efficiency in production and delivery.
Hokey and Gengui (2002) describes Supply Chain Modeling as function of one or more decision parameters: (Min, 2002)
- Location determines where the plants, manufacturing centers and warehouses are located along with their points of consolidation
- Allocation determines the supply of chain goods, in other words, which warehouses or DCs should serve which customers, market segments and suppliers
- Network Structuring considers centralization or decentralization of a distribution network and determines optimal combination of suppliers, plants, warehouses and consolidation so that supply can be phased out. This is part of management's decision on timing of expansion and/or elimination of DCs
- Number of facilities and equipment is a first level consideration on number of plants and DCs required to serve consumer demand in markets
- Number of stages determines the stages in a supply chain and may increase or decrease with horizontal integration or separation of stages in the chain
- Service Sequence is a factor that determines purchase volume of inputs, production and shipping volume depending upon production capacity and market demands of a good
- Inventory level is a consideration of inventory volume that includes amount of raw materials, finished products and stock keeping at each supply chain step.
- Size of the workforce is consideration of employee and labor engagement during the supply chain management process
NO PLAGIARISM POLICY - ORDER NEW 7108IBA SUPPLY CHAIN MANAGEMENT ASSIGNMENT & GET WELL WRITTEN SOLUTIONS DOCUMENTS WITH FREE TURNTIN REPORT!
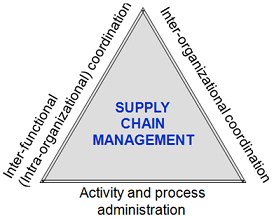
Effective supply chain management provides benefits to an organization's performance. It improves customer service by delivering the right product at the right location and on time. This therefore positively affects growth in organizational sales. The products are introduced in the markets at a quicker rate and supply of products and services are consistently maintained with an efficient supply chain. An effective management system would lower supply chain costs with reduction in cost of procurement of raw materials, transportation expenses, carrying costs and others, thus contributing to a firms' profitability.
Q1. The manufacturing plans at Cairns, Darwin, and Mandurah, the three manufacturing sites.
Answer - Supply Chain Management in Dronautics Ltd
Supply chain management in Dronautics Ltd. is faced with supply decisions from the three plants at Cairns, Mandurah and Darwin to the distribution centers at Adelaide and New Castle. Production costs, as mentioned earlier, differ at all three facilities and transport expenses are distinct in each route. The given transportation costs from manufacturing plants to DCs have been specified as follows:
Table 1
|
|
Per Pallet ($)
|
Per Unit ($)
|
|
Adelaide
|
Newcastle
|
Adelaide
|
Newcastle
|
Cairns
|
790.00
|
660.00
|
6.00
|
5.00
|
Darwin
|
530.00
|
920.00
|
4.00
|
7.00
|
Mandurah
|
790.00
|
1,190.00
|
6.00
|
9.00
|
Table 1 therefore shows that per pallet (and/or unit) transportation cost is lower from Cairns to New Castle compared to Adelaide whereas Darwin and Mandurah's expenses are minimized with supply to the Adelaide DC. In order to finally determine the cost effective supply route however from each plant to its distribution center, the production cost of the pallet/unit also needs to be considered. In other words, if production cost is much higher at one facility compared to another, then monetary benefits from cheaper transportation may be superseded. In case of Dronautics Ltd, a total cost of production has been calculated from production to delivery of drone products to the DC and has been shown below:
ENDLESS SUPPORT IN 7108IBA SUPPLY CHAIN MANAGEMENT ASSIGNMENTS WRITING SERVICES - YOU GET REVISED OR MODIFIED WORK TILL YOU ARE SATISFIED WITH OUR 7108IBA SUPPLY CHAIN MANAGEMENT ASSIGNMENT HELP SERVICES!
Table 2
Cost of Production & Transportation of Pallet from Manufacturing Plant to DC
|
Plant Locations
|
Per Pallet Production Cost at Plant
(240 units)
|
Cost Minimizing Supply Chain Route
|
Pallet Transport Cost to DC (given)
|
Total Cost per pallet
|
Cost Effectiveness of the Supply Route
|
Cairns
|
10320
|
Cairns to New Castle
|
660
|
10980
|
Low
|
Darwin
|
9600
|
Darwin to Adelaide
|
530
|
10130
|
High
|
Mandurah
|
10080
|
Mandurah to Adelaide
|
790
|
10870
|
Medium
|
So, as per details in table 2, the cheapest route identified is Darwin to Adelaide that can serve consumer markets delivery cost is lower. Darwin appears to be the most cost effective center of the three plants considering both production and transport. It is also clear that demand for drones in markets where delivery cost is lower from the Adelaide center can be fulfilled by production at Darwin or Mandurah only. However, optimal production decisions on number of units at the two centers can be split when information on center wise production capacity is available. Since such data is unavailable, it can be assumed that supply chain decisions would be based upon total cost of production and transportation as given in the table with the cheapest being Darwin to Adelaide and Cairns to New Castle.
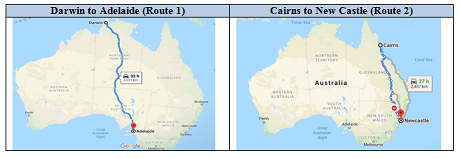
GET READYMADE 7108IBA SUPPLY CHAIN MANAGEMENT ASSIGNMENT SOLUTIONS - 100% PLAGIARISM FREE WORK DOCUMENT AT NOMINAL CHARGES!
Q2. The distribution network and the associated flows over the whole network.
Answer - Current Supply Chain Scenario:
Given cost considerations, Dronautics Ltd. would therefore consider supply from Cairns to New Castle as one of the supply routes and Darwin to Adelaide as another. Production at Mandurah would be limited to emergency conditions, to fill gaps and emergency requirements at the other two centers. Given the constraint that supply has to go through DCs and despite being the second best cost efficient option, production at Mandurah plant becomes redundant limiting the overall efficiency of supply chain and has been detailed in Table 3.
Demand for production at Cairns and Adelaide:
Total demand for production at Adelaide is 509 pallets and at Darwin is 368 pallets based on the number of consumer markets they shall be catering to. The consumer markets have been chosen with consideration of cost of delivery provided to each of the markets from the DCs. New Castle delivers to 7 points and Adelaide to 5 as described in the table.
Table 3
Plants
|
Unit Cost of Production $/Unit
(given)
|
Distribution Centers available
|
Consumer Markets chosen on the basis of low delivery cost
|
Aggregate Demand in Markets (Units)
Given data
|
Aggregate Dd in Pallets =Aggregate Demand/240 (approx)
|
Cairns
|
43
|
New Castle
|
Sydney
|
50,230
|
209
|
|
|
|
Brisbane
|
49,360
|
206
|
|
|
|
Gold Coast- Tweet Heads
|
6,790
|
28
|
|
|
|
New Castle - Maitlands
|
4,870
|
20
|
|
|
|
Canberra - Queanbeyan
|
4,580
|
19
|
|
|
|
Sunshine Coast
|
3,330
|
14
|
|
|
|
Wollongong
|
3,020
|
13
|
|
|
|
Total
|
122,180
|
509
|
Darwin
|
40
|
Adelaide
|
Melbourne
|
49,360
|
206
|
|
|
|
Perth
|
20,590
|
86
|
|
|
|
Adelaide
|
13,460
|
56
|
|
|
|
Hobart
|
2,330
|
10
|
|
|
|
Geelong
|
2,680
|
11
|
|
|
|
Total
|
88,420
|
368
|
MOST RELIABLE AND TRUSTWORTHY 7108IBA SUPPLY CHAIN MANAGEMENT ASSIGNMENT HELP & HOMEWORK WRITING SERVICES AT YOUR DOORSTEPS!
Q3. How rational is the policy that products have to go through the distribution centers? If this could be changed, what changes you would like to propose? What results you would expect to see?
Answer - Rationality of Products being distributed through DCs
Distribution centers provide organized support on delivery that manufacturing units strictly meant for production may not be able to handle. However such considerations are better analyzed through cost and delivery times (Supply Chain Resource Cooperative). Decisions on whether DCs are necessary may be assessed on the following factors:
- SCM considers flow of goods and services between the point of origin and consumption to satisfy customer requirements.
- Time and place utility need to be considered in the logistics of the process.
- Impact of the markets at the locations and disparate business expectations also influences the logistics of SCM.
In case of Dronautics Ltd, the market in Perth is very close to the Mandurah plant compared to Adelaide and New Castle. Cost of delivery from Adelaide to Perth is 860 AUD/pallet and 1060 AUD/pallet from New Castle to Perth. This is therefore an additional cost borne by the company for the restriction of goods to be delivered from DCs only. Not only is the distance factor reduced along with time to delivery with direct delivery option from Mandurah plat to Perth but associated expenses for meeting the demand at the Perth consumer market is reduced. Perth is the fourth best market with demand of 20,590 units of drones (86 pallets approx) with an estimated delivery expense of 860 per pallet which totals to 73,960 AUD. This cost would be dramatically reduced if direct deliveries from Mandurah to Perth were allowed based on location preferences. Although the cost of production is slightly higher at Mandurah than Darwin, the extra $2 per unit of production (compared to Darwin) is compensated with savings in transportation and time. This conclusion assumes that the Mandurah plant is capable of handling delivery of manufactured pallets as efficiently as the Adelaide plant with minimum additions to production cost.
Q4. How much will be the cost difference, if breaking down of pallets (i.e., taking products from fully packed pallets) is allowed?
Answer - Breaking down of Pallets
Breaking down of the pallets would be necessary when demand in consumer markets slightly exceeds or falls back on drone requirements that are not fulfilled by discreet pallet numbers. Since unit costs are consistent with costs of pallet delivery (that is cost of pallet and unit delivery are consistent) from plants to DCs and further from DCs to markets, the supply chain would therefore resort to the same routes as earlier for delivery of additional units. However with pallets broken down to units for delivery, the supply chain would incur much higher costs. For 240 units from Cairns to New Castle and Darwin to Adelaide, the estimated transport cost difference (on the pallet size) in the first phase is:
Table 4
|
Per Unit Cost of Delivery
|
Per Pallet Cost of delivery
|
Cost Difference for 240 units (pallet size)
|
Cairns to New castle
|
$5 per unit
|
$660
|
540 AUD
|
Darwin to Adelaide
|
$4 per unit
|
$530
|
430 AUD
|
HELPING STUDENTS TO WRITE QUALITY 7108IBA SUPPLY CHAIN MANAGEMENT ASSIGNMENT AT LOW COST!
This is will again be added to the cost difference in transportation from DC to the markets in the second phase. Table 5 here gives details on estimated cost savings with pallet delivery as opposed to units.
Plants
|
Unit Cost of Production $/Unit
|
Distribution Centers
|
Markets
|
Aggregate Demand in Markets (Units)
|
Cost Difference in the Second Phase (DC to Markets)
|
Cairns
|
43
|
New Castle
|
Sydney
|
50,230
|
23022
|
|
43
|
|
Brisbane
|
49,360
|
55530
|
|
43
|
|
Gold Coast- Tweet Heads
|
6,790
|
7639
|
|
43
|
|
New Castle - Maitlands
|
4,870
|
1015
|
|
43
|
|
Canberra - Queanbeyan
|
4,580
|
3053
|
|
43
|
|
Sunshine Coast
|
3,330
|
4440
|
|
43
|
|
Wollongong
|
3,020
|
2013
|
Darwin
|
40
|
Adelaide
|
Melbourne
|
49,360
|
78153
|
|
40
|
|
Perth
|
20,590
|
60054
|
|
40
|
|
Adelaide
|
13,460
|
2804
|
|
40
|
|
Hobart
|
2,330
|
10485
|
|
40
|
|
Geelong
|
2,680
|
4243
|
|
|
|
|
Phase 2
TOTAL SAVINGS
|
252452
|
The cost difference in the second phase here has been calculated as follows:
Cost Difference = [ (no. of units) * (per unit cost of delivering units to the marketing site)] - [(no. of pallets) * (cost of delivery to the marketing site per pallet) ]
There is huge market turnover with pallets being delivered instead of units. Pallets donot require extra packaging, wrapping and handling which units do and hence unit deliveries shall introduce inefficiencies in the system. It is therefore in the interest of managers to emphasize on group deliveries of products in all industries where the cost advantages related to economies of scale can be captured.
SAVE DISTINCTION MARKS IN EACH 7108IBA SUPPLY CHAIN MANAGEMENT ASSIGNMENT WHICH IS WRITTEN BY OUR PROFESSIONAL WRITER!
Q5. Assess whether it will be worthwhile if Dronautics relocates its production to either Adelaide or Newcastle.
Answer - Relocation Strategy
An evaluation of the supply chain logistics of Dronautics Ltd suggests that relocation to New Castle would be a profitable consideration in the relocation strategy as all the 7 market points under New castle would be covered inclusive of New Castle-Maitlands. Such relocation would also be in favor of Adelaide but in this case, the demand for goods in the consumer market is lower covering only 5 points. A difference in transport savings for about 141 pallets would occur with relocation to New castle (509 pallets in demand) compared to Adelaide (368 pallets in demand). In addition, the cost of production in New Castle ($32 per unit) is lower than Adelaide ($33 per unit).
Q6. If the production relocation is profitable, which site should be chosen? How much would be the cost saving? If the production location is not profitable, by how much should the annual operating cost reduce so that it will be attractive to Dronautics again?
Answer - Estimated Savings from Relocation
Estimated savings from relocation would stem from transport cost saved from delivery to New Castle from Cairns on 509 pallets and reduced cost of production at New Castle at $32 per unit as shown in table 6. As relocation appears to have huge benefits, there is no requirement of reduction in annual operating cost. Savings from relocation however also needs to be weighed with infrastructural investment cost in opening up a new manufacturing facility that is beyond the scope of this study. If investment costs can be realized over a certain period of time, such a relocation strategy in case of Dronautics Ltd would definitely be advisable.
Table 6 - Estimated savings in relocating to New Castle
Transport cost saved from Cairns to New Castle on 509 pallets in AUD
|
335940
|
Cost of Production saved (Cost of production at Cairns - Cost of production at New castle) for 509 pallets in AUD
|
5599
|
Total - Estimated savings (AUD)
|
341539
|
HIRE PROFESSIONAL WRITER FROM EXPERTSMINDS.COM AND GET BEST QUALITY 7108IBA SUPPLY CHAIN MANAGEMENT ASSIGNMENT HELP AND HOMEWORK WRITING SERVICES!
Q7. Discuss the impact of production relocation to cycle and safety stocks, try to pick appropriate parameters to estimate the effect.
Answer - Safety Stock Cycle
In a globalized economy, inventory management is one of the largely prioritized operations in multinational and medium sized companies. Inventories can be of two types - cycle stock that acts as buffer between delivery and replenishment of stock and safety stock covers for sudden changes in market demand when peaks are balanced along with demand variations. Careful inventory management is essential for maintaining standards of delivery and setting the risk safety or cycle stock could prove to be very essential in SCM.
In an effort to reduce stock levels, companies engage in reducing safety stock to zero to cut down on costs. However this affects service levels that go down with sudden peaks in the market. A mathematical assumption that relates safety stock to optimal numbers is:
SafetyStock = Z(service level) * √(AvgLt * StDevDemand2 + AvgDemand2 * StDevLT2)
The equation illustrates that safety stocks depend on service levels and variations in demand and lead times. If safety stocks are set at zero then both the other factors (service and variations in lead time and demand) should also have a z score of zero. This implies that zero stock levels would definitely lower service standards. This equation does not however take into account failure rates, reorder periods and order quantity requirements.
Q8. Construct at least one other possible scenario, and discuss your findings.
Answer - Implications of Safety Stock Cycles in Relocation & Example
|
Lead Time
|
Standard Dev
|
Location A Supplier
|
15 days
|
10 days
|
Location B Supplier
|
24 days
|
1 day
|
Location A and B supplier need to safeguard their inventory for 25 days as per requirement. But when safety stock calculations are done from the equation, supplier B would be required to maintain a lower safety stock simply because of a higher lead time so that the cycle stock can cover for the demand within the 24 days timeline. A 15 days lead time for location A may not provide the same guarantee for cycle stock to satisfy the customer requirement. This explains how variability in lead times can affect the safety stock from different locations and during relocation a company needs to assess such potential differences in lead time if safety stocks appear to have additional cost considerations for the company. With no variability, there is no requirement of a safety stock.
WE HELP STUDENTS TO IMPROVE THEIR GRADES! AVAIL TOP QUALITY 7108IBA SUPPLY CHAIN MANAGEMENT ASSIGNMENT HELP AND HOMEWORK WRITING SERVICES AT CHEAPER RATE!
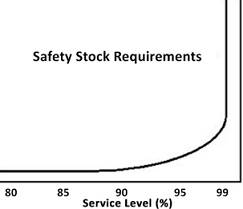
Variability is however an uncertain factor and leaving lead time of suppliers open without proper forecast in demand. If the variability factor is minimized, stock requirements would automatically reduce to zero. Conversely with inaccurate predictions, there could be excess safety stocks or stock outs.
Inventory management is a critical component of SCM. It is required to "meet anticipated demand", "smooth production requirements", "protect against stocks", "take advantage of order cycles", "a hedge against price increases", "permits operations" and "decouples components of the production system" (Polienere, 2015).
Relocation decisions have to be therefore based on logistics related to production transfer and criticalities. The time required to move the manufacturing base from the old factory site to the new one may have to drops in production levels as the old one is shut down. Sometimes it becomes impossible to move equipment from location to another within a short period of time and the company has to bear losses with the stall in production.
A critical component is the time planning that makes planning of relocation very difficult. Management of various stages need particular attention with needs analysis, identification and finalization of the new area, land acquisition or settlement issues, transfer of key employee base, new permits, authorizations in a new location, city or county, hiring of new labor force and complete shifting of the dynamics related to the manufacturing process. An entirely new business plan needs to be therefore drafted before such relocation can be planned. Financial management is an integral part of this -- access to credit or use of capital supports the framing of the business plan at a fair and affordable price whether it is with an entirely new location or an existing location where expansion is necessary.
The conclusion to this research is there is no single defined guidelines to a company's decision on relocation but such a move may be necessary given logistical issues, higher cost factors and inventory problems related to a particular site. The choice of the location should support organizational goals on efficiency of supply chain management and is therefore a long term strategic decision for a company.
Dronautics Ltd is a wonderful case study to illustrate the Supply chain management process and in determining the supply routes, cost effective measures in optimization of the delivery process with adjustments in delivery routes as per demand requirements in Australian drone market.
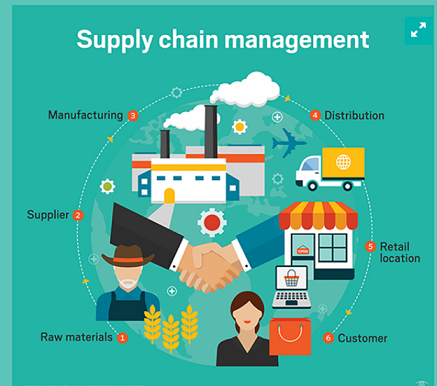
NEVER MISS YOUR CHANCE TO EXCEL IN 7108IBA SUPPLY CHAIN MANAGEMENT ASSIGNMENT! AVAIL AFFORDABLE AND RELIABLE 7108IBA SUPPLY CHAIN MANAGEMENT ASSIGNMENTS HELP SERVICES OF EXPERTSMINDS.COM!
Avail the Griffith University, Australia Assignment Help Service for its related units and courses such as:-
- 7100IBA Applied Project Assignment Help
- 7103IBA Global Business Logistics Assignment Help
- 7104IBA Legal Aspects of Procurement Assignment Help
- 7106IBA Managerial Problem Solving Assignment Help
- 7105IBA Strategic Sourcing Assignment Help
- 7102IBA Strategic Supply Chain Management Assignment Help
- 7107IBA Sustainable Supply Chain Management for the Next Decade Assignment Help
- 7117IBA Business Intelligence Systems Assignment Help
- 7116IBA Data Resource Management Assignment Help
- 7113IBA Enterprise Mobility Assignment Help